1.Introduction
Drilling is a complex and crucial operation in the oil and gas industry, as well as in other fields such as geothermal energy extraction and water well construction. The process involves creating a deep hole in the earth's crust to access valuable resources. Along with specialized equipment, a variety of chemicals play essential roles in ensuring the efficiency, safety, and success of the drilling operation. This article outlines the detailed drilling process and the key chemicals used at each stage.
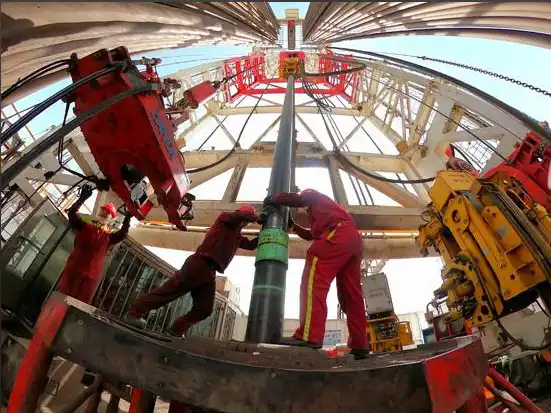
2.Pre - drilling Preparation
- Site Selection and Survey: The first step is to identify a suitable drilling site. Geologists conduct extensive surveys using techniques such as seismic imaging, gravity and magnetic surveys, and well - log analysis from nearby existing wells. This helps in determining the potential location of oil, gas, or other resources. Once the site is selected, the area is cleared of any obstacles, and access roads are built to facilitate the transportation of equipment and materials.
- Well Design: Engineers design the well based on the geological data and the objectives of the drilling operation. The design includes determining the well's depth, diameter, and trajectory (vertical, deviated, or horizontal). Considerations are also given to factors such as the type of formations to be drilled through, the expected pressure and temperature conditions, and the need for casing and cementing to support the wellbore.
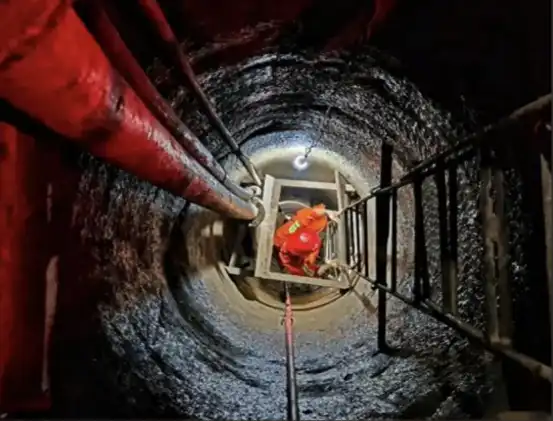
2.2 Surface Hole Drilling
- Setting up the Rig: A drilling rig is erected at the site. The rig consists of various components, including a derrick for hoisting and lowering the drill string, a power source to drive the drilling equipment, and a mud system for circulating drilling fluid. The drill string, which is a series of connected pipes, is assembled and lowered into the wellbore.
- Initial Drilling: The drilling process begins with the use of a large - diameter bit to drill the surface hole. This hole is typically shallower and is used to install the surface casing. The surface casing provides structural support to the wellbore, prevents surface water from entering the well, and serves as a guide for subsequent drilling operations. During this stage, drilling fluid, also known as mud, is continuously circulated through the drill string and out of the bit. The mud cools and lubricates the bit, carries cuttings (rock fragments) to the surface, and helps to maintain the stability of the wellbore.
2.3 Intermediate and Production Hole Drilling
- Changing Bits and Casing: As the well is drilled deeper, smaller - diameter bits are used to drill through different formations. Intermediate casing is installed at appropriate intervals to reinforce the wellbore and isolate different formations. This helps in controlling pressures and preventing the collapse of the wellbore. The drilling process continues, with the mud system constantly adjusting to the changing conditions of the formations being drilled.
- Directional Drilling (if applicable): In some cases, especially for offshore drilling or when targeting specific reservoir zones, directional drilling techniques are employed. This involves using special downhole tools to control the direction of the drill bit, allowing the well to reach the desired location in the subsurface. The drilling fluid plays a crucial role in directional drilling by providing the necessary lubrication for the drill string to bend and change direction.
2.4 Completion and Testing
- Cementing: Once the well has reached the desired depth, cementing is carried out. Cement is pumped down the annulus (the space between the drill string and the wellbore or between different casings) to seal the wellbore and bond the casing to the surrounding rock. This provides additional support to the wellbore, prevents fluid migration between different formations, and helps in isolating the production zone.
- Well Completion: After cementing, the well is completed. This may involve installing production tubing, wellhead equipment, and other components necessary for the extraction of oil, gas, or other resources. The well is then tested to determine its productivity and to ensure that it meets the required safety and quality standards.
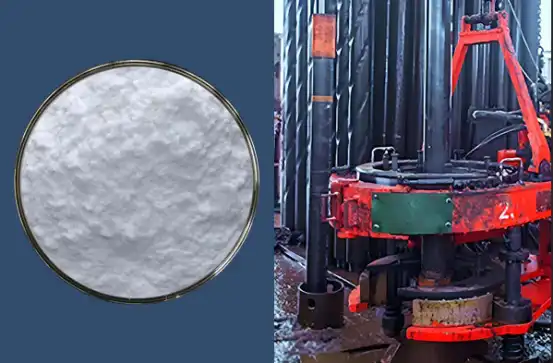
3.1 Drilling Fluid Additives
- Viscosifiers: Viscosifiers are added to the drilling fluid to increase its viscosity. This helps in suspending cuttings and preventing them from settling back into the wellbore. Common viscosifiers include bentonite clay, xanthan gum, and carboxymethyl cellulose (CMC). Bentonite clay, a type of swelling clay, absorbs water and forms a gel - like structure that increases the viscosity of the drilling fluid. Xanthan gum, a polysaccharide produced by bacteria, is highly effective in maintaining viscosity even under high - temperature and high - shear conditions.
- Weighting Agents: Weighting agents are used to increase the density of the drilling fluid. This is important for controlling the pressure in the wellbore and preventing formation fluids (such as oil, gas, or water) from flowing into the wellbore. Barite (barium sulfate) is the most commonly used weighting agent. It has a high specific gravity and can be easily added to the drilling fluid to adjust its density as needed. Other weighting agents include hematite and ilmenite.
- Filtrate Reducers: Filtrate reducers are added to the drilling fluid to minimize the amount of fluid that filters into the formation. This helps in maintaining the stability of the wellbore and preventing damage to the formation. Polymers such as polyanionic cellulose (PAC) and synthetic polymers are commonly used as filtrate reducers. They form a thin, impermeable filter cake on the wall of the wellbore, reducing the fluid loss.
- Lubricants: Lubricants are added to the drilling fluid to reduce friction between the drill string and the wellbore wall. This helps in preventing wear and tear on the drill string, reducing the torque required to rotate the drill string, and facilitating the movement of the drill string in the wellbore. Mineral oils, synthetic esters, and surfactants are used as lubricants in drilling fluids.
3.2 Cement Additives
- Accelerators: Accelerators are added to the cement slurry to speed up the setting time of the cement. This is important in some situations, such as when rapid cementing is required to prevent the collapse of the wellbore or to resume drilling operations quickly. Calcium chloride is a common accelerator used in cementing. It reacts with the cement components, promoting the formation of hydration products and accelerating the hardening process.
- Retarders: Retarders are used to slow down the setting time of the cement. This is useful when the cementing operation is complex and requires more time for pumping the cement slurry into the wellbore. Lignosulfonates and certain organic acids are commonly used as retarders. They interact with the cement particles, delaying the hydration reactions and extending the setting time.
- Dispersants: Dispersants are added to the cement slurry to improve its flowability. They help in reducing the viscosity of the cement slurry, allowing it to be pumped more easily through the wellbore. Polycarboxylate - based polymers are widely used as dispersants in cementing. They adsorb onto the surface of cement particles, preventing particle agglomeration and improving the fluidity of the slurry.
3.3 Other Chemicals
- Corrosion Inhibitors: Corrosion inhibitors are used to prevent the corrosion of the drill string, casing, and other metal components in the wellbore. The presence of water, oxygen, and acidic gases (such as carbon dioxide and hydrogen sulfide) in the wellbore can cause corrosion. Organic compounds such as imidazolines and amines are commonly used as corrosion inhibitors. They form a protective film on the metal surface, preventing the contact of corrosive substances with the metal.
- Bactericides: Bactericides are added to the drilling fluid and cement slurry to control the growth of bacteria. Some bacteria can cause corrosion of metal components and can also affect the properties of the drilling fluid and cement. Chlorine - based compounds and quaternary ammonium compounds are used as bactericides. They kill or inhibit the growth of bacteria, ensuring the integrity of the drilling operation.
4. Conclusion
The drilling process is a multi - stage operation that requires careful planning and execution. Chemicals play a vital role at every stage of the drilling process, from the initial drilling to the completion of the well. Drilling fluid additives help in maintaining the performance of the drilling fluid, cement additives ensure the proper setting and bonding of the cement, and other chemicals such as corrosion inhibitors and bactericides protect the equipment and materials used in the drilling operation. The proper selection and use of these chemicals are essential for the safe, efficient, and successful completion of drilling projects.