1. Introduction
Foam is a dispersion system composed of gas - filled bubbles separated by thin liquid films. While foam can be desirable in some applications such as food and cosmetics for its texture - enhancing properties, in many industrial and domestic processes, excessive foam can cause significant problems. Defoaming, the process of reducing or eliminating foam, is crucial in these situations. Defoamers, also known as anti - foaming agents, play a central role in achieving effective defoaming. This article explores the diverse applications where defoaming is necessary and the classification of defoamers.
2. Applications of Defoaming
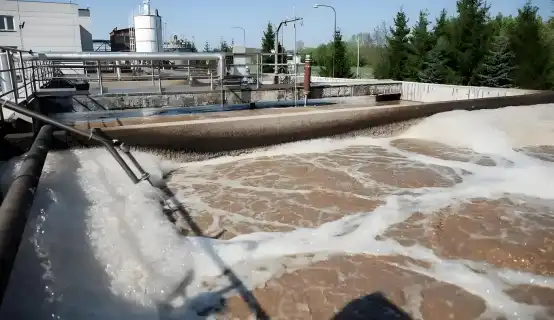
2.1 Industrial Applications
- Chemical Industry: In chemical manufacturing processes, foam can impede operations. For example, in the production of polymers, foam formation during polymerization reactions can lead to inconsistent product quality. Excessive foam in reactors may also cause overflow, resulting in material loss and potential safety hazards. Defoamers are added to control foam, ensuring smooth reaction progress and high - quality product output. In the production of paints and coatings, foam can cause defects such as pinholes and craters on the painted surface. Defoamers are used to eliminate foam during the manufacturing process and also when the paint is being applied, ensuring a smooth and defect - free finish.
- Food and Beverage Industry: Although foam is sometimes desired in products like beer and whipped cream, in many food and beverage production steps, it can be a nuisance. During the fermentation process of beer, foam control is essential to prevent overflow in fermentation tanks. Defoamers are carefully selected to ensure they do not affect the taste or quality of the final product. In the production of fruit juices and syrups, foam can form during concentration or bottling processes. Defoamers are used to remove this foam, preventing product spillage and maintaining product clarity.
2.2 Domestic Applications
- Laundry: Foam can be a problem in laundry detergents, especially in high - efficiency washing machines. Excessive foam can reduce the washing efficiency and cause mechanical problems in the washing machine. Defoamers are added to laundry detergents to control foam, ensuring proper cleaning and preventing foam - related issues.
- Dishwashing: Similar to laundry, excessive foam in dishwashing liquids can be inconvenient. It can overflow from the sink and make the cleaning process messy. Defoamers are incorporated into dishwashing products to limit foam generation, making dishwashing more efficient and less messy.
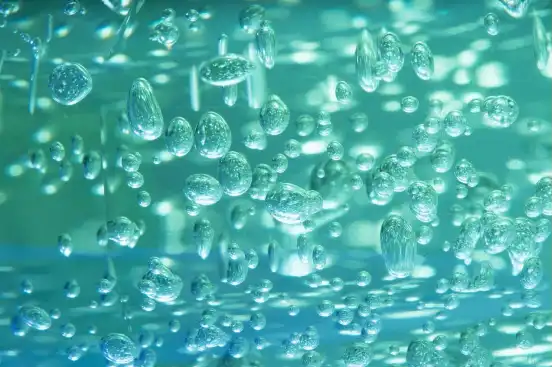
3. Classification of Defoamers
3.1 Based on Chemical Composition
- Silicone - based Defoamers: Silicone defoamers are widely used due to their excellent defoaming performance. They are typically composed of polydimethylsiloxane (PDMS) and its derivatives. PDMS has a low surface tension, which allows it to quickly spread on the surface of foam bubbles, causing the bubbles to burst. Silicone defoamers are highly effective in a wide range of applications, including industrial processes, food and beverage production, and water treatment. They are also heat - resistant and chemically stable, making them suitable for use in high - temperature and harsh chemical environments. However, in some applications where strict regulations on silicone residues exist, such as in certain food - contact applications, their use may be restricted.
- Mineral Oil - based Defoamers: Mineral oil defoamers consist of mineral oils with additives. The mineral oil acts as the main defoaming component by spreading on the foam bubble surface and disrupting the liquid film. These defoamers are relatively inexpensive and are commonly used in applications where cost is a major consideration, such as in some industrial processes. They are also effective in controlling foam in aqueous systems. However, their performance may be affected by the presence of surfactants in the foaming medium, and they may have a relatively short - lived defoaming effect compared to some other types of defoamers.
- Polyether - based Defoamers: Polyether defoamers are made from polyether polymers. They work by adsorbing onto the foam bubble surface and changing the surface properties of the bubble, leading to defoaming. Polyether defoamers are particularly suitable for applications where compatibility with the foaming medium is important, such as in some food and beverage applications. They are also biodegradable in some cases, making them more environmentally friendly compared to some other defoamer types. However, their defoaming efficiency may vary depending on the specific chemical structure of the polyether and the nature of the foaming system.
3.2 Based on Mode of Action
- Antifoaming Agents: Antifoaming agents are defoamers that prevent the formation of foam. They work by interfering with the surface - active agents in the foaming medium. For example, some antifoaming agents can adsorb onto the surface - active molecules, reducing their ability to form stable foam films. Antifoaming agents are often added to systems at the beginning of a process to prevent foam from forming in the first place.
- De - foaming Agents: De - foaming agents, on the other hand, are used to break down existing foam. They act by rapidly spreading on the surface of foam bubbles, causing the liquid film to rupture. De - foaming agents are typically used when foam has already formed and needs to be quickly eliminated. In some cases, a combination of antifoaming and de - foaming agents may be used for comprehensive foam control in a process.
3.3 Based on Physical Form
- Liquid Defoamers: Liquid defoamers are the most common form. They are easy to handle and can be easily added to the foaming medium. Liquid defoamers can be formulated as emulsions, solutions, or suspensions, depending on the specific application requirements. They are suitable for a wide range of applications, from large - scale industrial processes to domestic products.
- Solid Defoamers: Solid defoamers are less common but are useful in some specific applications. They are often in the form of powders or granules. Solid defoamers can be added directly to the foaming system, and they gradually release the defoaming components as they dissolve or disperse in the medium. They are particularly suitable for applications where slow - release of the defoaming agent is desired, such as in some long - term storage or continuous - process applications.
4. Conclusion
Defoaming is an important process in various industrial and domestic applications to address the problems caused by excessive foam. The classification of defoamers based on chemical composition, mode of action, and physical form provides a wide range of options for different applications. The selection of the appropriate defoamer depends on factors such as the nature of the foaming medium, the application requirements, and any regulatory constraints. By understanding the applications of defoaming and the classification of defoamers, industries and consumers can effectively control foam and improve the efficiency and quality of their processes and products.